ڤيتوجراوت اي ار 717
جراوت إيبوكسي وراتنج حقن.
Vetogrout ER717 is a low viscosity epoxy resin-based grout for crack injection where the hardened grout’s chemical resistance and physical properties are of extreme importance (for example: extreme industrial applications, rail tracks, dynamic load situations, chemical tanks, etc.). Vetogrout ER717 consists of two components (Base and Hardener) that are provided in the right proportions. When mixed and applied, it penetrates deep into cracks and cavities, providing a permanent seal.
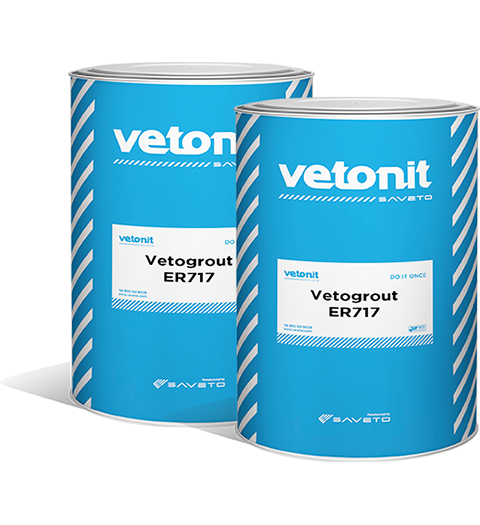
الاستخدامات
- To restore structural integrity of structural elements.
- To inject structural elements in retaining walls, beams, columns, shear walls, tanks, etc.
- For grouting and static crack filling from 0.2 to 10 mm.
- For base plate grouting in dynamic load situations.
المزايا
- Used in a wide range of situations such as cyclic and dynamic load cases.
- It is highly durable, ensuring long working life with high mechanical properties such as compressive, flexural, and tensile strength.
- Cost-effective with rapid strength gain ensuring minimum structural downtime.
- Non-shrink and complete surface bonding providing a 100% effective bearing area.
- It withstands hydrostatic pressure and prohibits penetration of contaminants and aggressive chemicals
تعليمات الاستخدام
Keep the unrestrained surface area of the grout to a minimum.
Generally, the gap between the perimeter form-work and the plate edge should not exceed 75mm on the pouring side and 25mm on the opposite side. Keep form-work on the flank sides tight to the plate edge. Provide air pressure relief holes to allow venting of any isolated high spots.
The form-work should be constructed to be leak-proof as Vetogrout ER717 is a free flow grout. To achieve this, use mastic sealant or a rubber gasket seal beneath the constructed formwork and between joints.
For free flow grout conditions, it is essential to provide a hydrostatic head of grout. To achieve this, use a feeding hopper system.
The substrate must be free from oil, grease, or any loosely adherent material. If the concrete surface is defective or has laitance, it must be cut back to a sound base. Bolt holes or fixing pockets must be blown clean of any dirt or debris.
If a delay is likely before placing steel base plates, it is recommended that the underside and edge are coated with Vetoprime EP490 to prevent rust formation and ensure bonding with the Vetogrout ER717.
Clean all metal surfaces to a bright finish following the Swedish Standard SA 21/2 or equal. Apply Vetoprime EP490 directly onto newly cleaned steel surfaces even if they are damp.
All cracks must be chased and open to a 2mm thickness (width generated by a saw blade).
Remove laitance and roughen 2 cm on each side of the crack using a hand grinder, then clean the surface and all cracks with compressed air.
Depending on the injection method (surface nipples or injection packers); the surface nipples on the crack face should be fixed using Vetorep ER350 (a twin-pack epoxy putty and leveling compound) before sealing the crack surface with Vetorep ER350. You can also seal the crack surface directly before drilling injection holes at 45-degree angles on the crack’s sides.
Pour the entire contents of the hardener container into the base container and mix for 2 - 3 minutes or until a uniform color is achieved. Once mixed, the material must be used within the specified pot life (see under Properties). After this time, unused material will have stiffened and should be discarded.
Note: All surfaces must be dried right before placement.
Ensure that the grout can be placed within its pot life.
Continuous grout flow is essential. Sufficient grout must be available before the start, and the time taken to pour a batch must be regulated to the time taken to prepare the next one. In the case of under-plate grouting, pouring should be from one side of the void to eliminate air entrapment.
The hydrostatic head must be maintained at all times so that a continuous grout front is achieved. In case of crack injection, consult your Saveto representative for a detailed method statement, onsite training, support, recommendation, or a specialty-approved applicator (if needed).
Use Vetonit Solvent XX400 to clean equipment before material begins to harden; otherwise, mechanical means will be necessary to remove hardened material.