Vetogrout UR710
Hydro-reactive polyurethane injection resin (foaming & flexible).
Vetogrout UR710 is a fast and highly reactive polyurethane foam producing resin that is specially used to temporarily stop water. It reacts when in contact with water to form a flexible closed cell foam barrier inside concrete cracks. Vetogrout UR710 is a two-component urethane injection system consisting of foam resin and an accelerator. The product is re-injectable with Vetogrout UR711 to form a permanent elastic seal in structural elements.
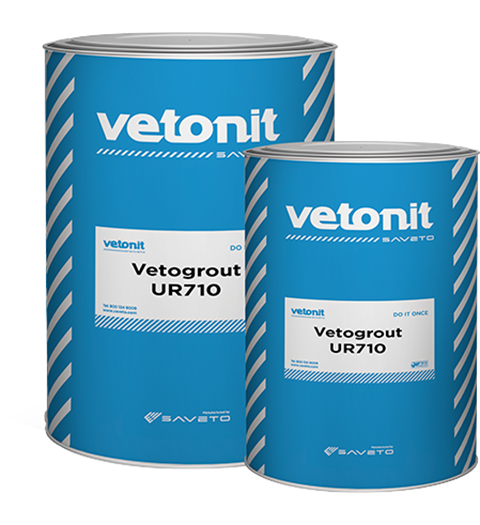
Uses
- Stopping crack seeping water.
- Injection of structural elements in water retaining or water excluding structures.
- Crack injection to stop water flow in retaining walls, manholes, reservoirs, etc.
Advantages
- Fast reaction time stopping flowing water under pressure.
- Re-injectable with polyurethane injection resin (Vetogrout UR711).
- Flexibility allows for movement accommodation in live cracks.
- Longer time to clean equipment compared to the market standard.
Usage Instructions
If water flow permits, clean the surface adjacent to the cracks and remove any dust, unsound or contaminated material, plaster, oil, paint, grease, corrosion deposits, or algae.
Preferably, prepare the surface using high-pressure water jetting or light abrasive blasting, followed by thorough washing to remove dust and remaining particles. Remove dirt with wire brushes or similar mechanical means.
Remove oil and grease deposits by steam cleaning, detergent scrubbing, or the use of a proprietary degreaser. Assess the effectiveness of decontamination by a pull-off test.
Blow the cracks and treat the surface with oil-free air to ensure complete removal of all dust and loose particles.
Fix the injection packers inserted into pre-drilled holes at intervals along the length of each crack. The distance between each packer will depend upon the width and depth of the crack. Spacing shall be close enough to ensure that the resin will penetrate along the crack to the next point of injection. This will normally be between 200mm to 500mm.
Seal the cracks’ surface between the packers with a band of Vetorep ER350, 30mm to 40mm wide and 2mm to 3mm thick. Seal both sides of any cracks which go all the way through a wall or slab in the way.
Please note: Where water flow is severe, omit the Vetorep ER350 application. In the case of a crack all the way through the wall or slab, locate packers on both sides, with those at the back placed at midway points between those at the front.
Where applicable, allow Vetorep ER350 to cure for 8 hours at 35°C. At low ambient temperatures (5°C to 12°C), extend the curing time, and ensure the epoxy putty surface seal has adequately cured before continuing.
Attach one end of the injection hose to the lowest packer on vertical cracks or the end of horizontal cracks. Treat each crack in a single, continuous operation.
Prepare sufficient material to be ready before the commencement of the work.
Thoroughly mix the accelerator with the base resin.
Take care to exclude moisture as much as possible and place it in an enclosed container after mixing. There will be skin on the surface, but the liquid underneath will be satisfactory for use.
Vetogrout UR710 should be used with standard injection equipment having closed containers. When flowing water has stopped, re-inject with Vetogrout UR711 to give a permanent seal. See Vetogrout UR711 datasheet.
Remove the packers or nipples. Make good any holes or voids with Vetorep ER350 and allow them to cure.
The epoxy putty can be ground off or softened with a blowlamp and peeled off. Do not allow to burn.
Remove Vetogrout UR710 and Vetorep ER350 from tools, equipment, and mixers with Vetonit Solvent XX400 immediately after use. Remove hardened material mechanically.