Vetogrout CG510 - AE
Multipurpose, universal, cementitious, non-shrinking grout.
Vetogrout CG510 is composed of Portland cement, special aggregates, and shrinkage-controlled, high-performance additives. It is supplied as a dry powder in pre-weighed bags that produce a cohesive mix when mixed with clean water on-site. Vetogrout CG510 is a premium, non-metallic, chloride-free, high-strength product that’s designed for grouting & anchoring. It can be applied generally at a thickness of 10 mm to 100 mm as a flowable paste, and at a thickness of 5 - 50 mm as a mortar paste.
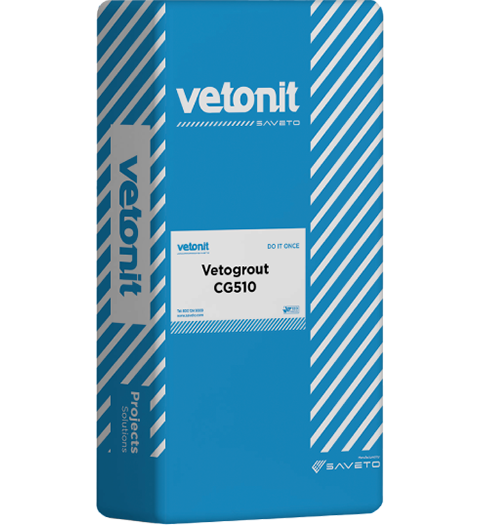
Uses
- For grouting & anchoring structural steel & precast concrete members.
- For filling voids & tie-rod holes.
- For under-plate grouting & light machine beds.
- To Anchor a wide range of fixings such as anchor bolts, stanchion bases, masts, and fence posts.
- Pile cap head treatment.
Advantages
- Factory-controlled pre-blend ensures consistent high quality.
- Requires only the addition of water on-site at the time of use.
- Chloride-free, High early & ultimate strength, and low permeability (This ensures the durability of the hardened grout).
- Exhibits high physical & mechanical properties.
- Non-shrinkage characteristics.
- Gaseous expansion system compensates for shrinkage and settlement (in plastic state).
Usage Instructions
The surface should be sound, clean, & free from loose material, grease, laitance, dirt-curing compounds, etc. Wet the substrate to achieve a saturated & surface dry condition before applying Vetogrout CG510.
Erect a hopper system and a form-work, make sure that the shuttering is watertight using a polyurethane sealant (such as Vetoflex PU780) or a rubber gasket seal. This step is important to ensure no cement paste and water leak from the shuttering.
Contact Saveto’s local representative for more technical information, the grouting detailed method statement, and CAD details.
The base plate must be clean and free from oil, grease, or scales. Air pressure relief holes should be provided to allow venting of all isolated high spots. If you’re using leveling shims, remove them after the grout has hardened. They also should be treated with a thin layer of grease.
Generally, the gap width between the perimeter formwork and the plate edge should not exceed 150 mm on the pouring side, and 50 mm on the opposite side. It is advisable (where practical) to have no gap at the flank sides.
For best results, use a mechanically powered grout mixer. For quantities up to 50 kg, use a slow speed drill fitted with a high shear mixer. Larger quantities will require a high shear vane mixer.
Do not use a colloidal impeller mixer. To enable smooth and continuous grouting, a sufficient mixing capacity and labor should be available. The application may require a grout holding tank (it’s important to gently agitate the grout).
Measure the selected water content accurately in the mixer. Slowly add the entire contents of the Vetogrout CG510 bag, while mixing, for 5 minutes. This will ensure that the grout has a smooth, even consistency.
Place the grout within 30 minutes of mixing to activate the full benefit of the expansion process. Vetogrout CG510 can be placed in thicknesses up to 100 mm in a single pour (when used as an under-plate grout).
To minimize heat build-up in thicker sections, it is necessary to fill out Vetogrout CG510 with well-graded & silt-free aggregate (Typically a 10 mm aggregate works fine). Any bolt pockets must be grouted separately before grouting the area between the substrate and the base plate.
Continuous grout flow is essential. Prepare sufficient grout before starting. Match the time needed to pour to the time needed to prepare the next one.
Upon completing the grouting process, cover the exposed areas well with polyethylene sheets to prevent evaporation of the mixture water for the first 24 hours.
Later, cure the grouted area using clean water twice a day for 3 days. Or you can use the Vetocure XT425, a waterbased curing compound (after placing the grout).
Clean Vetogrout CG510 off all tools with clean water immediately after use. Clean cured materials mechanically.