Vetotop EL492 - AE
Self smoothening epoxy based floor topping from 0.8 to 2 mm thickness.
Vetotop EL492 is a two-component high-performance self smoothening epoxy flooring system that flows in a honey-like manner to self smoothen to a perfect level. Once cured, the product has excellent abrasion and chemical resistance. Vetotop EL492 provides an attractive, hard-wearing, and easily cleanable floor finish. Its use on floors will enhance the lighting in the environment due to the product’s reflective properties.
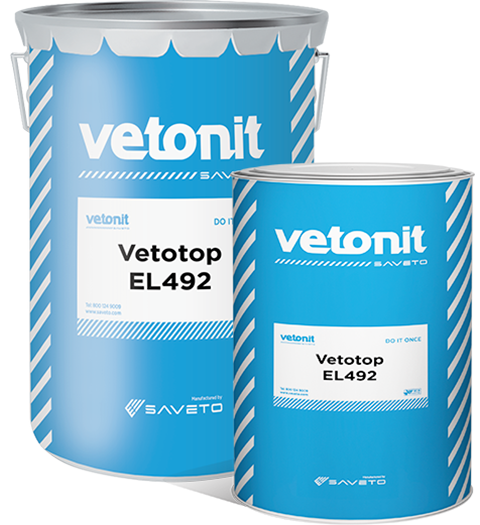
Uses
- Industrial kitchens and food processing plants.
- Vehicle factories and car parks.
- Clean rooms and laboratories.
- Plant rooms & pathways.
- Any flooring where impact resistance is required.
Advantages
- Two components; no dusting at the site.
- Fast, easy application; only 2 components to mix.
- High abrasion and chemical resistance.
- Low maintenance costs.
- Hygienic, impervious, and easy to clean.
- Available in 8 standard colors with the possibility of custom RAL colors.
- High bond, stronger than concrete cohesive strength.
Usage Instructions
The surface should be sound, clean, free from loose material, grease, laitance, dirt curing compound, etc.
Laitance and weak surface layer shall be removed using mechanical methods such as grinding or blasting to provide a sound, well-profiled surface. Repair all necessary areas before application by using epoxy mortar from the Vetorep ER range.
New concrete floors shall be at least 28 days old with a moisture content of less than 5% (shall earlier application be required testing of substrate for moisture conditions shall be made).
All surfaces receiving Vetotop EL492 should be primed with Vetoprime EP491, designed for maximum absorption and adhesion to concrete substrates. Add the entire contents of the hardener tin to the base tin and mix the two primer components thoroughly for at least 3 minutes - only mix full packs.
Once mixed, the primer should be applied immediately to the prepared substrate using stiff brushes and/or rollers. The primer should be well ‘scrubbed’ into the substrate to ensure full coverage. Still, take care to avoid over-application or ‘ponding.’ Allow the primer to dry before proceeding to the next stage, do not proceed whilst the primer is ‘tacky’ as this will lead to unsightly marks in the finished surface.
Porous substrates may require a second primer coat - when the first coat is directly absorbed into the substrate - but observe a minimum over-coating time.
Vetotop EL492 is supplied in two pre-weighed packs (base and hardener), ready for immediate on-site use. Part mixing of these components is not acceptable and will affect both the performance and appearance of the finished floor. Mixing should be carried out using either a forced action mixer; or a heavy-duty mobile mixer fitted with a jiffy type mixing paddle.
All such equipment should be of a type and capacity approved by Saveto. The components should be mixed in a suitably sized mixing vessel. Stir the base and hardener components individually, then empty them into the mixing vessel scrapping the edges and mix for 3-4 minutes until a completely homogeneous material is obtained.
Ensure sufficient labor and materials to make the mixing and subsequent application process a continuous one for any given, independent floor area. Once mixed, use the material within its specified pot life. The material should be poured onto the prepared and primed substrate as soon as mixing is complete. It should be spread to the required thickness using a notched trowel or a gauged spreader, with care taken not to overwork the resin, spreading evenly and slowly.
After laying, roll the material immediately using a spiked nylon roller to remove slight trowel marks and assist air release. The rolling should be carried out using a ‘back and forth’ technique along the same path. An overlap of 50% with adjacent paths is recommended. Further light rolling may be required to remove surface imperfections or for subsequent release of trapped air but should be before the setting of the product.
Follow all existing expansion or movement joints through the new floor surface. Joint sealant & joint geometry should be compatible with the floor type used, intended exposure conditions, and likely movement characteristics of the substrate - consult the local Saveto office for more details.
Vetoprime EP491 and Vetotop EL492 should be removed from tools and equipment with Vetonit Solvent XX400 immediately after use. Hardened material can only be removed mechanically.
The service life of a floor can be considerably extended by good housekeeping. Regular cleaning may be carried out using a rotary scrubbing machine with a watermiscible cleaning agent at temperatures up to 35°C.
- Vetotop EL492 should not be applied on surfaces known to, or likely to suffer from, rising dampness, potential osmosis problems, or have a relative humidity greater than 75%.
- In areas where the significant thermal shock is likely to occur, e.g., cold rooms, etc., please consult the local Saveto office.
- Vetotop EL492 should not be applied to asphalt, weak concrete below 25 N/mm2 compressive strength, unmodified sand/cement screeds, PVC tiles or sheets, or substrates known to move substantially, e.g., steel walkways.
- Vetotop EL492 should not be installed at temperatures below 12°C or above 40°C. If in doubt or for application outside these temperature limits, please consult your nearest Saveto office.
- In common with all epoxy materials, some light shade changes may be experienced over the long term when placed in adverse exposure conditions.
- Any such change in shade is not regarded as being detrimental to performance.
DOWNLOADS
EXPLORE MORE PRODUCTS
Vetotop CL531 - AE
Premixed 8 to 20mm thick polymer modified cementitious self-leveling underlayment.