Vetoproof CM745
Elastomeric crack-bridging cementitious waterproofing membrane.
Vetoproof CM745 is a two-component flexible polymer acrylic modified cementitious waterproofing coating; it has unique crack bridging characteristics even after long term water immersion. The product is suitable for use and contact with potable water and can withstand negative hydrostatic pressure.
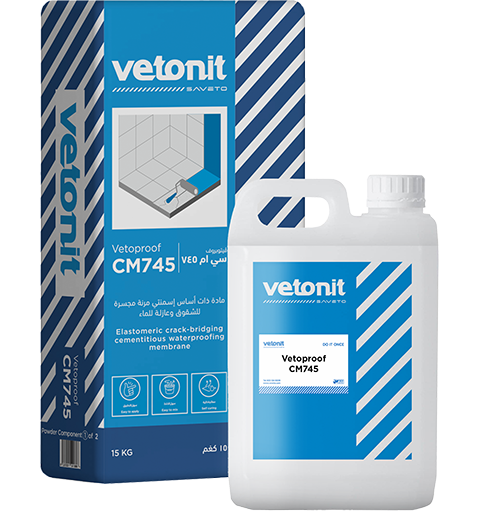
Uses
- Waterproof lining for water tanks, dams, canals,...etc.
- Covered roofs and wet-areas waterproofing while receiving tile adhesives.
- Protecting concrete and masonry structures against ingress of chloride ions and carbonation.
- Negative hydrostatic pressure resistance.
Advantages
- Non-Toxic - approved in contact with drinking water.
- Flexible, crack bridging.
- Ready to receive tile adhesives.
- Withstands high positive and negative hydrostatic pressures.
- Easy application by brush, roller.
- Bonds to damp concrete.
- Effective barrier to sulfates and chlorides.
- Excellent bond to concrete and masonry.
Usage Instructions
All surfaces should be dry and free from contamination, such as oil, grease, loose particles, decayed matter, moss algal growth, laitance, and all traces of mold release oils and curing compounds. This is best achieved by lightly grit-blasting the surface. Where moss, algae, or similar growths have occurred, treatment with a proprietary biocide should be carried out after the grit-blasting process. Remove spalled and deeply disintegrated concrete to sound concrete and repaired with a Saveto repair system.
If the surface contains small blow-holes, typically less than 1mm wide, the coating can be applied directly onto the substrate without the need for treatment.
Cracks that are less than 0.3mm in width can be over-coated as long as the crack is not likely to open up to greater than 0.3mm. Chased out cracks greater than 0.3mm in width to 4mm in width and approximately 15mm in depth; fill with Vetoproof CM745. When the material in the crack hardens, apply the coating over the crack.
Pour Vetoproof CM745 liquid concentrate from the plastic container into a suitably sized mixing container. Commence mixing with a propeller agitator attached to a slow speed drill (300-500rpm). Gradually, add the powder component to the liquid part to avoid lump formation and mix for 2-4 minutes. Immediately after mixing, use Vetoproof CM745. Do not mix material more than the quantity that can use within the pot life. Keep mixing Vetoproof CM745 during the application.
Thoroughly dampen the substrate surface with water using a brush roller or spray bottle. High porosity substrates will require more dampening than dense substrates. Do not apply the coating when the substrate is wet, but allow the water to soak until the substrate is just visibly damp before proceeding.
Remove any excess water using a sponge. Stop any running water with a suitable plugging mortar such as Vetoproof CR747. Contact the local Saveto office for further advice on other suitable water-stopping materials.
Vetoproof CM745 white should be applied as the first coat for optimum product use, with Vetoproof CM745 grey as the second coat. This gives a visual indication of coverage.
Apply the first coat at a wet film thickness of 1mm (approximate coverage per coat is 1.7 kg/m2 or 1 liter/m2).
To ensure achieving the correct thickness, measure out an area (for example, 200m2) then calculate how much material will be needed to cover this area. Monitor the coating thickness during application at regular intervals using a wet film gauge. During application, take care of filling the imperfections such as blowholes. If not, fill them while the coating is still in fluid status by using a dry sponge. If the coating dried before finding these imperfections, fill them using fresh material.
The exact drying time will depend on surface temperature, relative humidity, and air movement. High temperatures and/or low humidity will reduce the drying time. This can vary from 1 to 16 hours. Leave the first coat to dry until firm and non-markable to the touch. There is no maximum time between coats; however, the surface may need cleaning with water before applying the second coat to remove potential contamination.
Apply the second coat at a wet film thickness of 1mm. Pre-dampening of the surface is not necessary before applying the second coat.
However, Vetoproof CM745 is self-curing; it protects the freshly applied coating from rain and strong wind until it becomes firm to the touch.
The most suitable brush is a soft-bristled wallpaper paste brush (120 - 220mm wide). Where applied to larger areas, it is advisable to use a brush with a handle. Load the brush up well and spread the material to the required thickness. If the brush begins to drag during the application, do not add water to the material but dampen the surface again. Finish in one direction for a neat appearance. For floor application, a soft-bristled broom is recommended. Pour the material onto the substrate and then spread it to the required thickness.
Application by roller has the benefit of quick speeding over brush application, particularly on smooth substrates. A good quality medium hair roller is recommended. Load the roller well for ease of application.
A heavy roller will leave a pattern; therefore, it is important to use a finishing tool to produce a smooth coating with a uniform 1mm wet film thickness.
To produce a smooth finish or to repair film defects, use a finishing tool. Examples of suitable tools include a steel plastering trowel, a caulking tool, and a hard sponge. Use all those tools immediately after coating application; otherwise, the coating may drag or tear. When using a hard sponge, it should be dry or very slightly damp. Do not use a wet sponge, as this will cause the polymer to come to the coating surface, which will cause an unsightly white, streaky effect.
Carry out spray application using specialized pumping equipment (contact Saveto’s local office for more information). This is the preferred method for applications over 150 m2.
In smaller tanks with restricted access, it may be beneficial to use the spray application method. This means the material will be pumped into the restricted area rather than carrying it physically.
Follow the mixing procedure as previously described, taking extra care in mixing to ensure that no lumps remain in the mix. Place the mixing container on plastic sheeting to prevent contamination in the mix. Scrap the material from the mixing vessel above the wet line following every mix. Clean the mixing paddle to remove hardened material, which, if ingested, may cause blockage in the pump.
Pour the material into the hopper. Scrape the sides of the hopper down at regular intervals to prevent hardened material from contaminating the mix. Place a cover over the hopper to prevent product skinning caused by water loss.
Pump the mixed material through the hose to the spray gun. Adhere to the substrate preparation and coverage rates described above. Measure the wet film thickness using a wet film thickness gauge every 2 - 3 meters until the spray operator judges the ideal application speed and distance from the substrate. Re-spray any areas less than 1 mm thick. Subsequent film thickness measurements should be carried out approximately every 10m2.
Thoroughly dampen the substrate surface with water using a brush roller or spray bottle. High porosity substrates will require more dampening than dense substrates. Do not apply the coating when the substrate is wet, but allow the water to soak until the substrate is just visibly damp before proceeding.
Remove any excess water using a sponge. Stop any running water with a suitable plugging mortar such as Vetoproof CR747. Contact the local Saveto office for further advice on other suitable water-stopping materials.
Allow the Vetoproof CM745 to cure for at least 28 days before commissioning.
Immediately following the application, clean all tools and equipment with clean water. Hardened material can be removed by mechanical means.