Vetotop US364
High performance & solvent-free polyurethane screed (For heavy duty applications).
Vetotop US364 is a multi-component high-performance solvent-free polyurethane screed. Once cured, the product has excellent abrasion and chemical resistance, suitable for heavy-duty applications and thermal shock resistance. Vetotop US364 provides an attractive, hard-wearing, and cleanable floor finish supplied in a 15 liters kit. Vetotop US364 is used for car park flooring systems, industrial warehouses, logistics centers, freezer rooms. Vetotop US364 is applied in thicknesses between 4 - 15 mm.
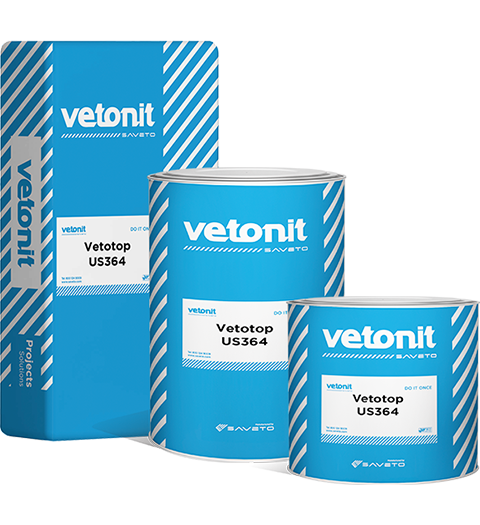
Uses
- Heavy-duty traffic such as car parks, ramps, industrial warehouses, logistical centers,...etc. u Mechanical and chemical exposure applications.
- Laboratories, hospitals, food and beverage industries.
- Freezer rooms and applications where thermal shock resistance is required.
Advantages
- Thermal shock resistance.
- High abrasion and chemical resistance.
- Low maintenance cost.
- Hygienic, impervious, and easily cleanable.
- High bonding properties (stronger than concrete cohesive strength).
Usage Instructions
The surface should be sound, clean, free from loose material, grease, laitance, dirt-curing compounds, etc.
Laitance and weak surface layers must be removed using mechanical methods such as grinding or blasting to provide a sound, well-profiled surface. Use an epoxy mortar from the Vetorep ER range to repair all necessary areas before applying.
New concrete floors should be at least 28 days old with a moisture content of less than 5% (test the substrate’s moisture conditions if an earlier application is necessary)
All surfaces receiving Vetotop US364 should be primed with Vetoprime EP491, designed for maximum absorption and adhesion to concrete substrates.
Add the entire content of the hardener tin to the base tin and mix the two primer components thoroughly for at least 2 minutes - only mix full packs. Once mixed, apply the primer immediately to the prepared substrate using stiff brushes and/or rollers.
The primer should be well ‘scrubbed’ into the substrate to ensure full coverage, but take care to avoid overapplication or ‘ponding.’ Allow the primer to dry before proceeding to the next stage, do not proceed whilst the primer is ‘tacky’ as this will lead to unsightly marks in the finished surface.
Porous substrates may require a second primer coat - when the first coat is directly absorbed into the substrate - but observe minimum overcoating times. Many applicators developed a practice where the first prime coat is dressed in sharp silica sand (0.5 to 1 mm aggregate diameter) and then reprimed once the excess material has been removed.
This practice is intended to increase bond strength and resist transverse shear through the development of mechanical keying. While Saveto does not object to such practices, it is important to reach the proper thickness of the polyurethane screed (Vetotop US364), excluding the thickness achieved by the priming and broadcast process.
Vetotop US172 is supplied in three pre-weighed packs (base, hardener, and aggregate) that are ready for on-site use. Do NOT mix partial quantities as it will affect both the performance and the finished floor’s appearance. Mixing using either a forced action mixer or a heavy-duty mobile mixer fitted with a suitable jiffy-type mixing paddle. The type & capacity of the equipment used should be approved by Saveto.
Mix the components in a suitably sized mixing container. Stir the base and hardener components individually, then empty them into the mixing vessel (scrape the edges) and mix for 2 minutes.
Slowly, add the content of the graded aggregate pack and mix for another 3 minutes until the mixture is completely homogeneous.
Make sure you have enough workers and ready materials to mix and apply in a continuous process for each floor area.
Once mixed, use the material within its pot life. Spreadthe material onto the prepared and primed substrate as soon as mixing is complete. Spread the material evenly and slowly to the required thickness using a notched trowel or a gauged screed box. Do not overwork the resin.
After laying, compact the material immediately using using a wood float or through the facilitation of an automatic resin trowel (helicopter). Screeding rods are useful in maintaining a minimum compacted thickness of 5 mm (5000 microns).
Vetotop US364 doesn’t allow fluids to cross through it when applied as a layer that’s 5 mm thick. Which is ideal in areas where wet areas are common and inconsistent and where a superb degree of cleanliness is necessary.
Seal the surface by mixing the base and hardener of Vetotop US364 (excluding the aggregate) and applying a seal coat.
Follow all existing expansion or movement joints through the new floor surface. Choose a suitable sealant from the Vetoflex sealant range.
Remove Vetoprime EP491 and Vetotop US364 from tools and equipment with Vetonit Solvent XX400 immediately after use. Remove hardened material mechanically.